High Alumina Checker Bricks
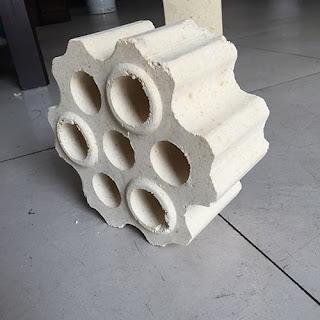
High alumina checker bricks have excellent thermal performance such as large heat storage area, smooth ventilation, and low resistance. It is also a heat transfer medium, mainly used for heat storage in the upper part of the regenerator of the hot blast stove. It plays an important role in the process of heating cold air into hot air. Features Has good volume stability. With high temperature load creep performance. High density, low porosity. High Alumina Checker Bricks Specifications Item RL-65 RL-55 RL-48 Al2O3 (%) ≥65 ≥55 ≥48 Refractoriness (℃) ≥1780 ≥1760 ≥1740 Refractoriness Under Load of 0.2MPa, ℃ ≥1500 ≥1470 ≥1420 Linear Change after Reheating, %, 1500℃x2h 0.1~-0.4 0.1~-0.4 0.1~-0.4 Apparent Porosity (%) 23 22 22 Cold Crushing Strength, MPa ≥50 ≥45 ≥40 Application It is mainly used for hot blast stoves. When the temperature is under 900℃, fire clay brick is used; while the temperature is higher than 900℃, the material of checker brick should be high alumina, mullite, sillimani